Affiliate disclosure: This post may contain affiliate links. Please see our Privacy Policy.
There’s a lot of nostalgia around maple syrup production, especially in Vermont. Much of the maple available these days is produced by large-scale farmers, with vacuum tubing systems and oil-fired boilers. Is there still a way to make a profit as a small-scale maple producer?
In the next few years, we plan to add maple syrup to our farm products, so this topic is near and dear to our hearts.
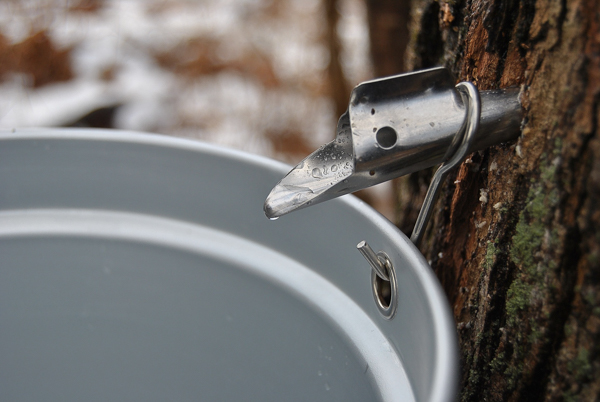
Vermont, in particular, is well suited to this, boasting the highest per tap syrup yield in the US, an average of roughly 25% higher than other states in New England in 2014. Vermont produced a gallon of syrup for every 3.24 taps.
The downside to high production is a lower price. Vermont taps more than twice as many trees as any other state but has one of the lowest average per gallon prices (second only to Maine) at roughly $35/gal for bulk wholesale in the past few years. Retail, however, is much more lucrative. We’ve seen local prices consistently in the $50-$60/gal range.
After a sugar bush survey, we estimate that we have roughly 150 mature sugar maples suitable for tapping within a short distance of the proposed sugar shack location. Based on average Vermont yields, 150 trees tapped should result in gross retail sales of $2,300-$2,800.
Now comes the fun part: figuring out costs. Upfront costs include collection equipment, be it buckets and taps or tubing, along with a sugar shack and arch.
These costs could be higher if you decide to go all out and invest in a fancy vacuum pump system or reverse osmosis filtration, but that’s hardly necessary at this scale. Ongoing cost includes fuel, labor and bottling.
Sugar Shack Costs
The cost of a sugar shack can vary widely, but for a 100-150 tap operation, our local extension recommends a simple 14×16 building, plus additional wood storage space.
A similarly sized structure built on our land this year cost $2,500 in materials and $1,800 in labor. We’re going to conservatively estimate $5,000 to build the sugar shack.
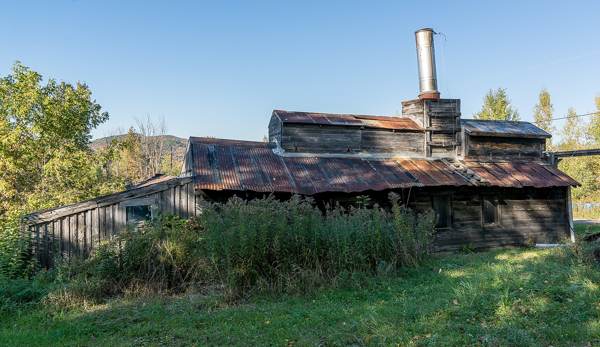
Cost of an Evaporator
The size of the arch needed depends on the number of taps and how much time you’re willing to devote to boiling each day. On a good day, each tap produces about a gallon of sap, so assuming we allocate 6 hours a day to boiling, we need an evaporator sized to boil 25 gallons per hour.
That puts us at the largest “hobby” sized boiler of 2’x6′ for roughly $4,500.
Maple Sap Evaporator Costs (as of 2015)
Evaporator Size 2’x33” 2’x4′ 2’x6′
Gallons Per Hour 5 15 25
Evaporator Cost (Approx.) $1,500 $3,800 $4,500
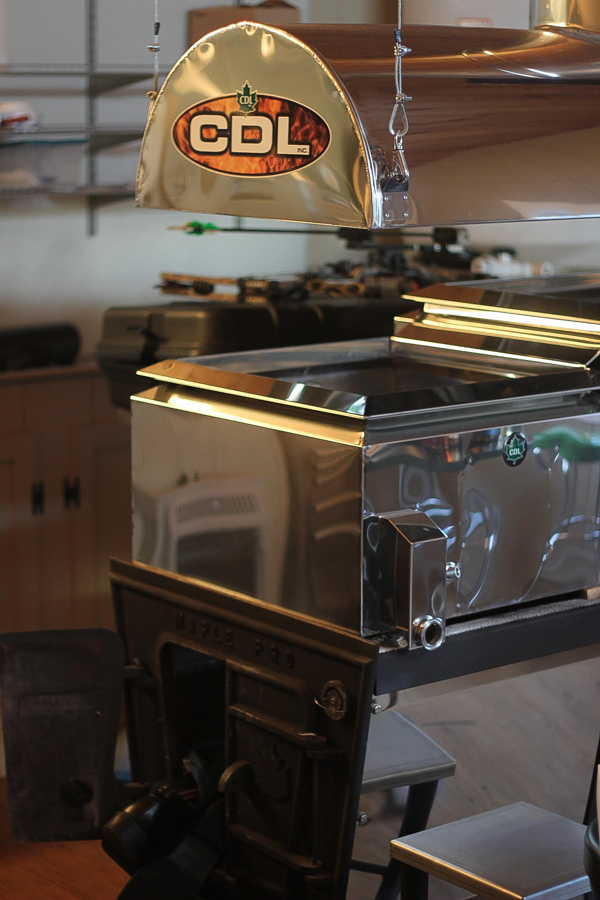
Costs of Maple Tapping Supplies
We’ve decided tubing, plastic taps and plastic bags are not an option for us for a number of reasons. First, we’d like to limit both our exposure to plastics and the amount of plastics diverted to the waste stream. Plastic bags need to be replaced every year, and plastic tubing has a 5-year lifespan, whereas stainless steel buckets and taps last indefinitely with proper care.
Tubing, while more convenient, presents a problem in our mixed-use sugar bush that is used extensively for forest gardening and recreation, and once set, the tubing stays strung through the woods year-round at head height for the duration of its 5-year lifespan.
Stainless steel taps bought in bulk are $1.85 each, or a total of roughly $280 for all 150. Buckets and lids are considerably more expensive at $23.80 each, or a total of $3,570 for all 150. All and all taps and buckets total $3,850.
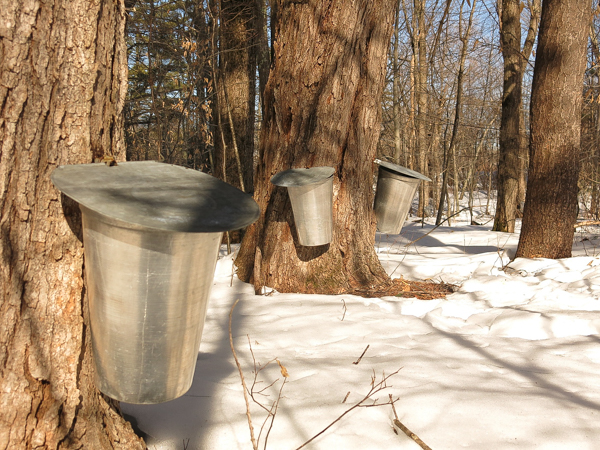
Costs for Wood or Fuel Oil
Next comes fuel selection. Generally, wood is the cheapest fuel option, even if you have to buy it rather than cutting it yourself. This year (2015), however, fuel oil is remarkably cheap due to various international tensions, while dry hardwood prices were averaging an unheard of $300 per cord (normally closer to $200).
2018 Update: Wood prices have continued to rise locally, and a dry cord of wood is often as much as $350 delivered. Green is $275 to $300.
It takes 4 gallons of #2 fuel oil to make 1 gallon of sap, which at this year’s prices would cost $12.
One cord of dry hardwood can make 20-30 gallons of syrup, but 30 gallons assumes high efficiency and very dry wood, so we’ll stick with 20 gallons for calculations here. The cost of a cord of wood divided by 20, so this year 300/20 gives you a cost of $15/gal of syrup.
Though I hate to admit it, it may actually be cheaper at this point to burn oil than wood.
In reality, those choosing to operate wood-fired boilers are not purchasing the wood. By and large, they’re cutting their own, which drastically lowers the cost per cord. They’re also usually burning wood that cannot be sold commercially because it’s not suitable for use in home wood stoves (hemlock, pine, etc).
In preliminary work thinning our sugar bush to allow more light for the maples, we cut roughly 10 cords of hemlock and white pine this summer. This quantity of wood barely even dented our abundant hemlock supply, and much more cutting is required before our sugar bush will be ready for operation.
While we can burn hemlock in an external wood boiler, 10 cords per year is way more than we need. Thus hemlock is a waste product of our sugar bush maintenance and it only makes sense to put it to good use rather than purchasing fuel oil.
Hemlock and white pine, however, contain fewer BTUs than hardwood. At 50% boiler efficiency and 20% moisture content in the wood, a cord of hemlock and white pine can produce 18 gallons of syrup starting at 2% sugar content, or 13 gallons starting at 1.5%. If we pessimistically assume 30% boiler efficiency those numbers change to roughly 11 and 8 gallons.
We’ll need somewhere between 2.5 and 6 cords of hemlock and white pine a year to support 150 taps.
Labor Required for Maple Syrup Production
Labor to maintain a bucket system and home-cut wood is going to add up to a lot of hours in a year. Woodcutting does take a lot of time, but in opening up pastures, maintaining our woodlot and thinning for permaculture plantings we’d be doing most of the same cutting anyway. Hemlock is not generally considered sale-able, thus our sugaring operation will be using the waste product of our other endeavors.
The Ohio state extension estimates that a 1000 tap operation requires 120 hours for tapping, gathering and cleanup in a tap and bucket operation. Our 150 taps will require a lot less labor, but there are definitely efficiencies of scale to be had, so we’ll assume 1/4 of the effort of 1000 taps and estimate 30 hours. On our 25 gallon per hour evaporator, we’ll need roughly 80 hours of boil time per season.
In total, a rough ballpark of man-hours puts us at 100-120 total hours.
Anyone who has ever spent time in a sugar shack in early spring in Vermont knows that boil time can hardly be considered “work.” This time of year cooking syrup and snowshoeing is the main form of recreation and social engagement available. There’s are very few other farm chores, and honestly little else to do.
While recruiting help for gathering sap buckets is sometimes a problem, there’s no shortage of volunteers around boiling time. Hours of lively conversation, hot cider and tank top weather around the arch-sauna late into the night attract all the neighbors. Thus, in reality, it’d be hard to ascribe more than ~40 hours of the 100-120 to “work”.
Since we won’t be hiring help, and it’s work we’ll enjoy in a time of year without much else to do, that makes labor costs very hard to pin down. At $10/hour, we could estimate our work somewhere between 40 hours ($400) or 120 hours ($1200).
Maple Syrup Bottling Costs
While fancy maple leaf-shaped jars are pretty and attract tourists’ attention. Generally fancy bottles more than recoup their costs when sold to the tourist market, but the problem is you need to have access to tourists.
Local Vermonters mostly buy their syrup in pint or quart mason jars, because they’re practical and reusable. Both jar sizes are currently selling for roughly $1 each. Our packaging costs would be roughly $250-300 annually.
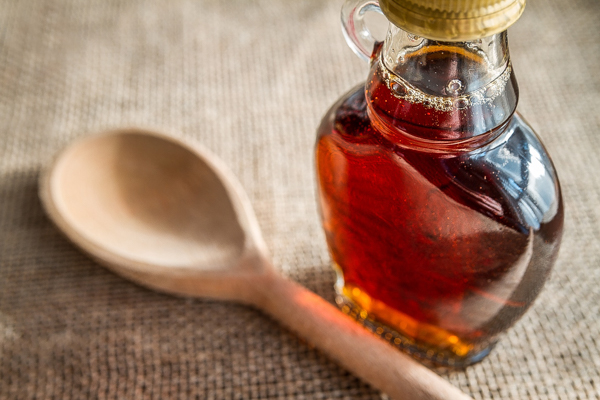
Total Costs for a Maple Syrup Operation
Upfront Investment
Sugar Shack: $5,000
Arch: $4,500
Buckets & Taps: $3,800
Total: $13,300
Annual Costs
Labor: $400-$1,200
Packaging: $250-$300
Annual Costs: $650 to $1,500
Gross Annual Sales
$2,300 to $2,800
Net Profits of A Maple Syrup Farm
How much does a maple syrup farmer make? The answer: not much.
Taking gross proceeds and deducting annual costs, our initial investment will be paid back in 7-13 years. We expect to be able to productively use this sugar bush and equipment for 30+ years, and ideally, transition it to our children.
All and all, does sugaring on this scale make sense as a financial venture with a profit motive? Not really. We’re talking small numbers here.
Net profits of $1,000-$2,000 per year don’t exactly pay the mortgage. However, there are many advantages to taking up sugaring and investing in the equipment.
1. It’s a hobby that keeps you in shape and provides for recreation in a time of year that’s otherwise bleak.
2. Though the net proceeds are low, it does pay for itself, which is something that can be said of few hobbies.
3. In the end, you have maple syrup and you’ve saved yourself the cost of a few months gym membership.
4. It allows for the productive use of one of our waste products, excess hemlock and white pine.
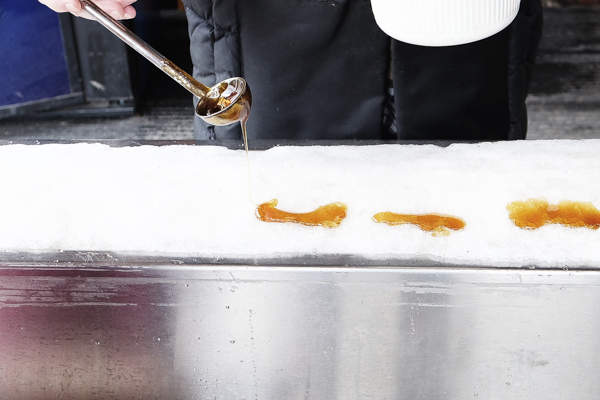
Sugaring in Vermont is recreation, pure and simple. Pouring your own syrup over your pancakes year-round just reminds you of how much fun you had boiling sap in the early spring with your friends, and selling sap just helps pay for that pleasure.
Making our own syrup is aligned with our value set, and fits in well with how we’d like to spend our time on this earth. As they say, if you love your work, you’ll never “work” a day in your life.
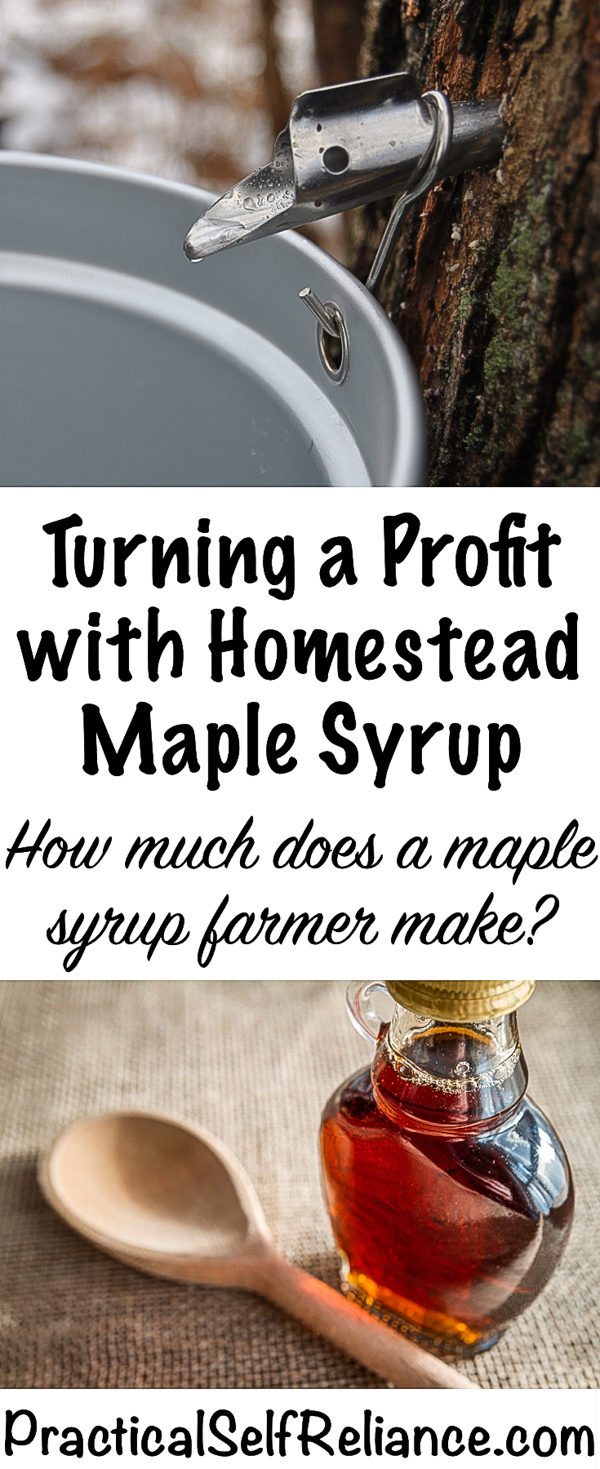
Sources
University of Vermont: Sugarhouse Design
Financial Analysis for Maple Syrup Production
I believe you did not include the procurement cost of firewood/fuel or the labor cost of splitting the 2.5 – 6 cords. This added expense further reduces profit margin to very minimal amount.
The post actually talks extensively about the cost of fuel along with the labor of cutting the wood. Most of the cutting as described is labor that they would be doing anyway to maintain their property but of course each situation is different. The update in the fuel section of the post does indicate that it might be cheaper to burn oil. This article can be a good starting point and then each individual person will need to adjust it according to their specific needs.
Hi, So how much would. 100 tap make during a season. How long is a season, would I need a worker if so how many. How big of an area would I need.? How much time per day would I have to put in. Anything else Im missing?
A lot of that depends on your area. Some areas will make more than others and the length of the season will also vary based on location. It takes somewhere around 100 to 120 man hours for the operation but much of that is boiling time.
Your estimates are kind of off. Used are much cheaper. You haven’t even begun with all the supplies need. Mason jars are the onlt practical way to go. Glass has gone through the roof. One advantage is keeping your land in agricultural use. Check with an accountant and ypur assessor fot tax advantages. Unless you are a big producer ,you do it because you like to. Selling sap. You still need a set up for a clean product. There needs to be a way to have it colle ted before it spoils. Prices vary. We had a 500 tap operation on vacuum. Lots of competion. Bulk sales are instant money without bottlung,but less money. With 150 taps, get by with good used equipment and sell to friends ,family and co workers. Been there done that.
Great article but not sure why you write off hemlock. You can mill it and use it for building if you have that much of it depending how accessible. Also the potential for increasing or decreasing maple prices can impact this as well as bartering but in VT its probably a hard item to barter depending on location! Cheers!
On our land at least, we’ve been told that our hemlock isn’t straight enough or big enough to be worth milling at scale. We’ve been considering a portable sawmill, and one day when we build a barn we likely will do that ourselves. We’re actually leaving the larger/straighter ones for that purpose, and the smaller/knotty/crooked ones are mostly feeding the maple boiler.
Hello, did you ever consider having someone collect the sap and make the syrup? If so, may have ask what they offer? We are considering buying an area with an estimated 4000 taps and were wondering whether it makes more sense to make the syrup ourselves or contract with someone to collect the sap and pay us a percentage of profits. Thank you, love your blog!
Charles
I’ve read in a few sources that the going rate to lease taps (which is what you’re talking about) is $1 per tap. They talk about this quite a bit in The Sugarmaker’s Companion, which is a recent publication. Personally, I’m not open to having people all over our land since we enjoy our privacy. Beyond that, I’m not open to having tubing up in my woods year round (they often leave it up for 5 years at a time year-round before replacement to save labor). For us, it’s not really an option because our house is right in the middle of our 30 acres, and we hike a lot on our land. That said, if I had a more remote parcel that might be worth considering, and it’s not a bad option in most circumstances.
With 4000 taps that’s not a bad side income in a year with no leg work in the woods. Good luck, hope it works out for you!
Thank you! I will read that book. I also don’t like having people tramping around my property , I am just concerned that we could handle 4000 taps. That’s a lot of work and equipment to buy. Thanks again.
Charles
Hi there. FYI. The bulk price for syrup is about $2.10 per lb. @ 11 lbs per gallon that’s $23.10 per gallon. NOT $35.00. Each tap will only produce 1 quart so based on 150 taps like you did that’s only 37.5 gallons that equates to $866.00. But you are correct that retail is where the money is but the market is flooded with that. Reminder. If you plan on retiring doing maple syrup. Good luck😀
Greetings from the Peace (NE BC and NW Alberta, Canada). Have you any feeling for how charcoal might work as a fuel for this? Potentially it allows one to collect some amount of the “yellow smoke” pollutants into “wood vinegar”, and hence potentially avoid emitting some things. And most processes of making charcoal seem to produce at least some charcoal which may only have value as an addition to compost or soil.
thanks ashley, nicely done article. i studied forestry at paul smiths college in new york. the college ran its own sugar bush and students participated via the minor forest products class. years later i work as a forester, and am looking to retire on a small farm or orchard. i am considering sugaring as part of the operation. your article is helpful with great resources. thanks!
Nice! I was in on my college’s forestry team, and we always got creamed by Paul Smiths at meets. You all take your forestry seriously up there. I really hope sugaring as part of your retirement works out for you, that’s part of our retirement plan too, since most of the costs are up front, if live long enough it’ll keep us healthy and eventually pay off and bring in a small profit each year.